Would it be good if Thailand is able to produce soluble sutures and reduce dependency on importing expensive medical products from abroad, for a better quality of life for people in the country, for patients to have lower- cost treatment options and minimize pain, as well as for doctors to avoid perform repeated surgeries.
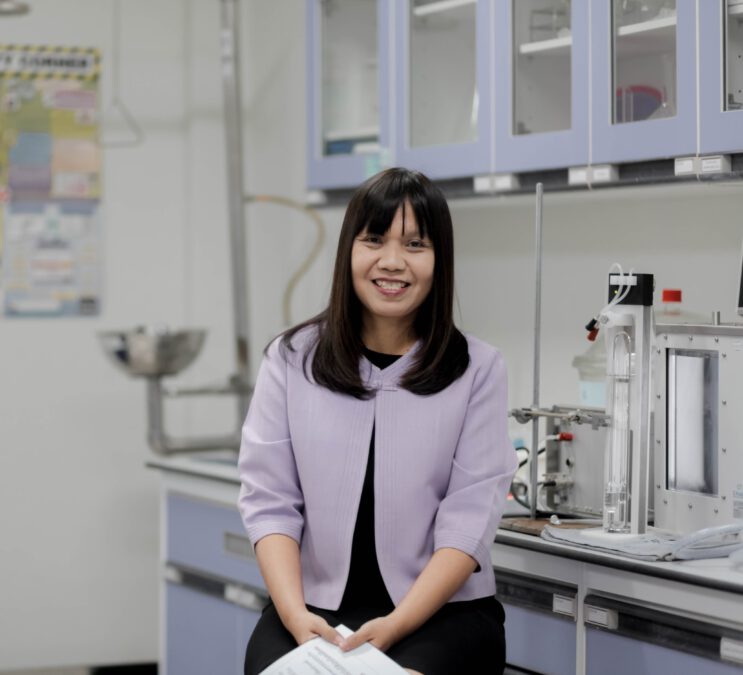
Assoc. Prof. Winita Bunyodom,Ph.D., Department of Chemistry, Faculty of Science, Chiang Mai University (CMU), head of the research project “Manufacture of commercial monofilament soluble sutures” under the push and support of Program Management Unit for Competitiveness (PMUC) Science, Research and Innovation Promotion Fund, said about the reason that the project was initiated that Thailand currently has to import 100% of the sutures used in the country from foreign countries, presenting very high cost. Normally,there are 2 types of imported sutures, ready-to-use and rolled. Therefore, we want to help the economy and Thai patients to have more treatment options.
Because Chiang Mai University is strong in research on biodegradable polymers made from corn, sugarcane and cassava, and is considered the only university capable of producing biodegradable plastics or polymers from agricultural raw materials for medical applications, covering all steps from upstream, midstream to downstream in ISO 13485 certified laboratories, which is a quality management system for medical devices, and is the first laboratory in Thailand to receive such standards.
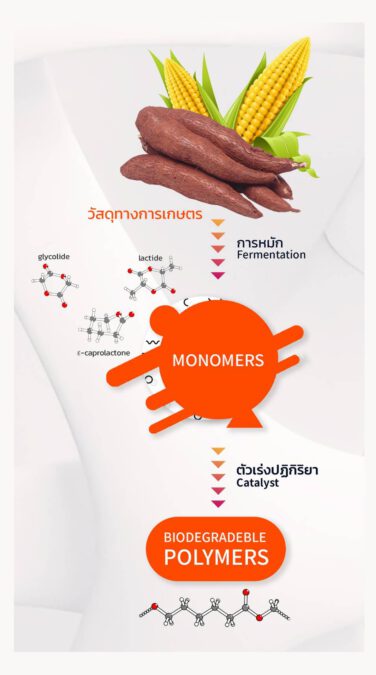
Making sutures from biodegradable polymers, which can slowly dissolve, helps the patient to not have to return for suture removal, and doctors to not have to perform the repeated surgery. Initially, the project was funded by NIA, PTT and IRPC with Nova Medic Co., Ltd., an importer of silk threads for sutures, serving as a consultant. The project has been in operation since 2019. It is expected that FDA certification as a medical device for commercial sale can be obtained by early 2023, after the results of the Clinical Trial Phase 1 were successful.
Assoc. Prof. Dr. Winita said that for the production of soluble sutures, we are producing medical grade resins or polymers with the development of a new high-efficiency catalyst. It can synthesize monomers or polymers in a short time span and at high purity in the laboratories, helping to reduce costs. This catalyst has a better control of object properties than other commercial catalysts we have used. It has already been patented both domestically and internationally, such as in China, the United States, Japan, Singapore and Europe. After producing plastic polymers, which are then formed into usable sutures, during the forming process, we must ensure the accuracy of the molding process, and must be able to produce it repeatedly. Then the preliminary properties must be tested for, after which bio-compatibility must also be tested in laboratory animals (rabbits, swines) successively. And finally, the human test, which is a clinical test.
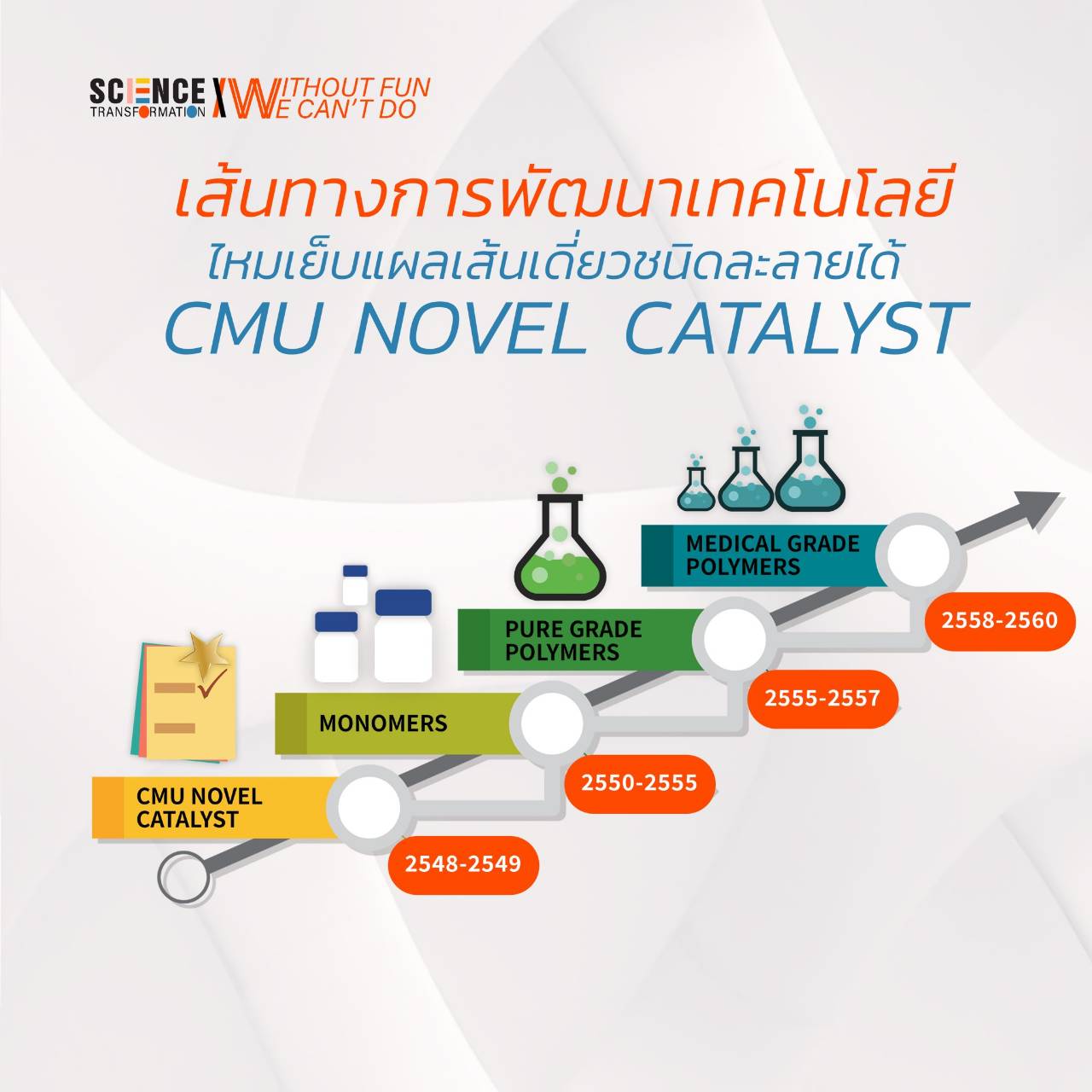
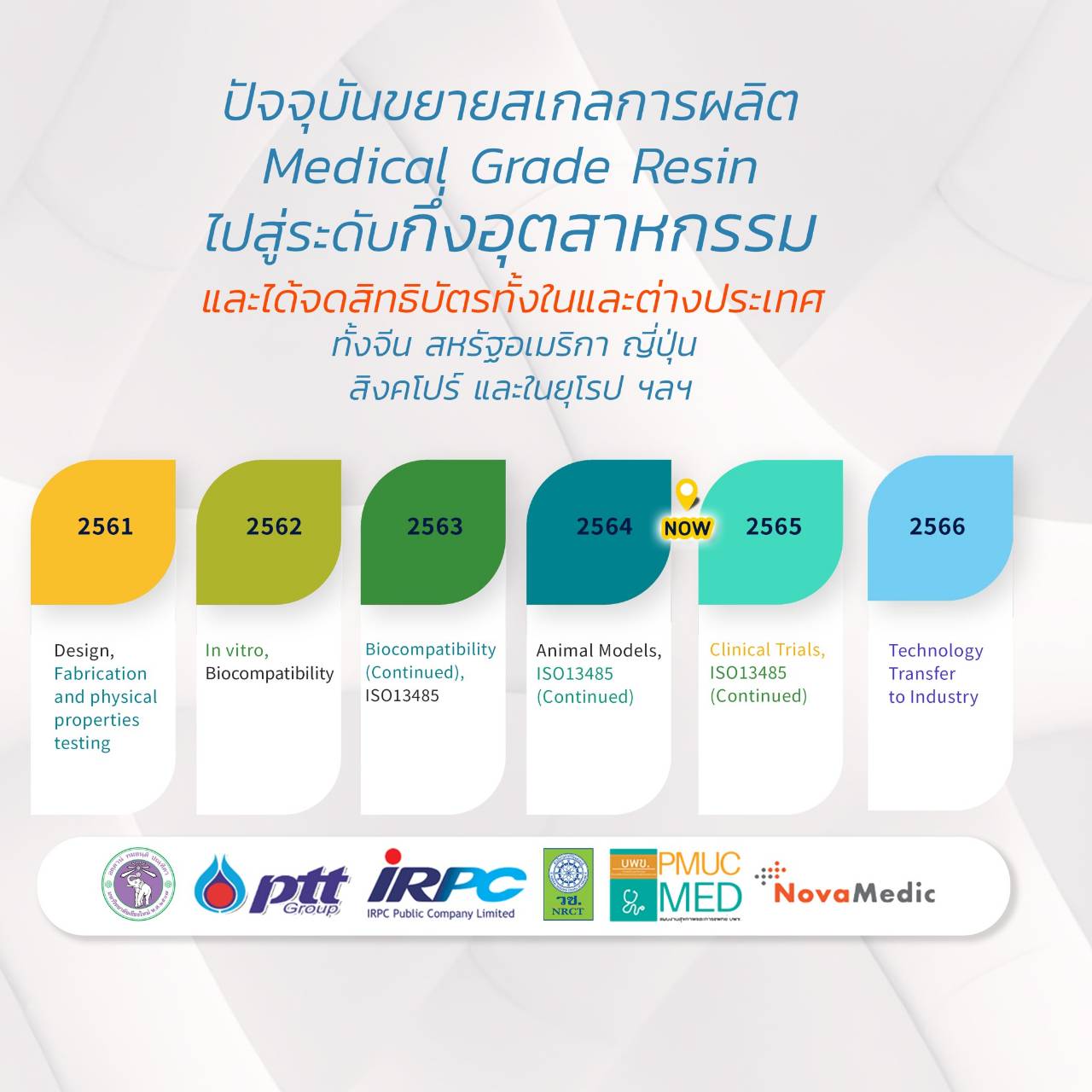
“Currently the lab trial is in the stage of preparation for the swine test which will begin in March. It takes approximately 6 months, after which a clinical trial will be conducted on 40 volunteer patients by the end of 2022. This trial is the first time in Thailand in which the invented soluble sutures have been tested in human, under the operation by the Faculty of Medicine, Chiang Mai University. The trial will divide volunteer subjects into 2 groups, one group using ordinary commercial sutures, and the other group using the invented sutures using random method to compare stitching by sutures in the subcutaneous layer to determine efficacy and safety levels, because the objective of the test to about dealing with infection. Also, there is a question whether the sutured wound will separate within 28 days after suturing, or whether there will be any complication within the succeeding 24 weeks or 6 months. It is important to see about doctors’ acceptance, as well as how long the sutures stay in the body. Typically, slow-dissolving sutures will stay in the body for about 6 months to 1 year, and eventually the suture must not be visible at all. Once FDA approval is obtained, it can be produced and sold commercially by 2023. Initially, it is expected that cooperative partnerships will be formed with small animal hospitals across the country, because each year a lot of stitches are used. By using silk that we developed ourselves in Thailand it should help the country realize quite some cost reduction. However, the question of using the technology to treat people, or which group it will be used for first, will depend on the policy of the PMUC committee, in joint deliberation with the industrial sector. But the most important thing is putting the sutures into practice must be well thought-out and error-free, and must be accepted by doctors and supported by the government.”
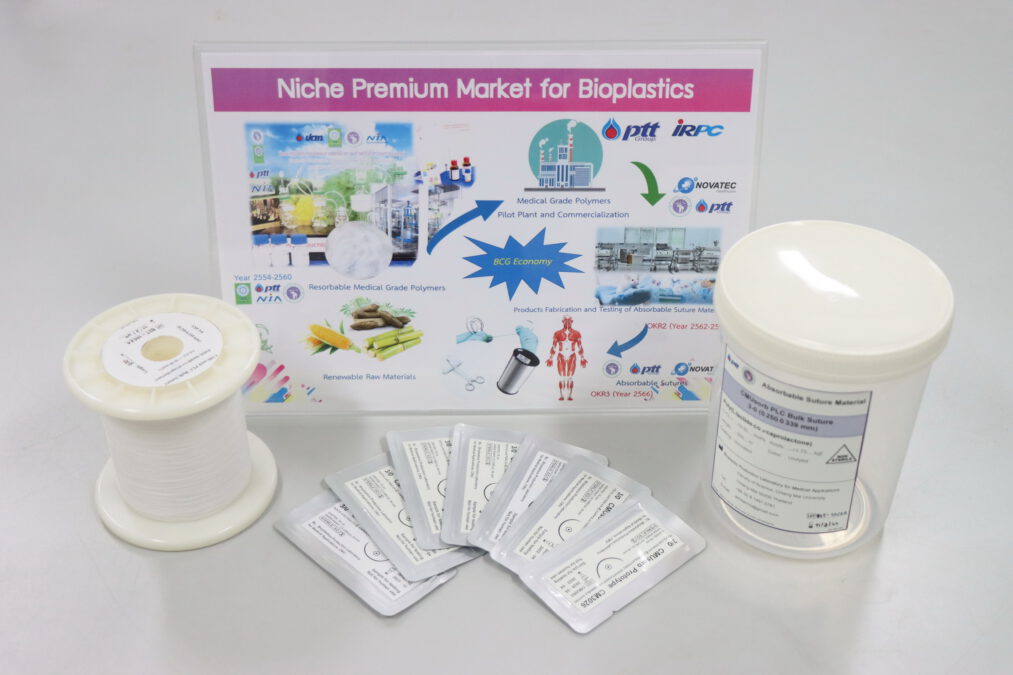
Assoc. Prof. Dr. Winita added that the reason it took more than 5 years of research and development is because suture medical devices are materials that are implanted in the human body and the decomposition process releases byproducts into the human body. Therefore, it is classified as a project in Class 4 with the highest risk. And the invented biodegradable polymer is the first in Thailand to be produced and sold from an ISO 13485 certified laboratory. It is half as cheap as imported polymers, at 7-9,000 baht per kilogram, compared to 200,000 baht per kilogram for imports. If this project is successful, in addition to greatly reducing the import of plastic polymers from abroad, it can also be further developed into other medical products. Further, if it is further developed to the finished product stage, it can reduce the import of medical devices and medical materials with high commercial value. It is another way to make medical expenses cheaper. and a better quality of life for Thai people.