On December 28, 2022, the Circular Economy Subcommittee, led by Dr. Pongwipa Lorsomboon, chairman of the subcommittee, and staff visited the area to inspect the implementation of the project for which the PMUC has provided research under the Circular Economy Plan in the past year at Kasetsart University, Bangkhen Campus, and Rajamangala University of Technology at Thanyaburi.
During the visit, the subcommittee inspected the progress of 3 projects in 3 industries, namely the packaging industry, textile industry and construction industry, as well as visited the laboratory for project implementation. Additionally there were discussions, brainstorming, and advice given on problem solving and operational suggestions to the research team.
Project to “Improve Performance and Quality of Recycled Polyethylene Terephthalate for Packaging Industry.”
Assoc. Prof. Amporn Saneh, Ph.D., and the research team from the Department of Packaging Technology and Materials, Faculty of Agro-Industry, Kasetsart University, collaborated with PTT Global Chemical Public Co., Ltd. to develop a production process for recycled plastic rPET to be effective in eliminating contaminants in PET packaging after use, and to develop innovations or new technologies to improve the properties of rPET for the production of rigid packaging such as bottles and trays. Moreover, effort has been made to analyze and monitor the efficiency of POSTC-PET contaminant removal during the recycling process in different recycling conditions, as well as to assess the safety of rPET for use as a food contact material. The goal is to help bring a huge amount of residual waste from PET plastic usage back into the recycling process and to help reduce the amount of residual waste in the country. Additionally it would also help to reduce resource consumption as well.
However, in reusing such plastics, it is necessary to take into account the safety and applicability of rPET, especially when being recycled into food contact materials. Therefore, for this research project an emphasis was placed on developing rPET for the packaging industry by studying the possible impact, quality issues, and potential contamination of packaging waste collected into the recycling system and how these factors affect the quality of the rPET. The ultimate goal is to be able to assess the efficiency of the contaminant removal process in the current recycling system in order to determine whether the resulting rPET is suitable for reuse in producing food contact materials.
From the trip to followup on this operation, it was found that the research team had completed more than 80% of the overall work. The research team was able to establish a complete recycling process and eliminate contaminants. And the next step is to compare with FDA criteria. In addition, the research team can enhance the properties of the rPET to be more suitable for commercial use in the production of food contact materials. Currently there is an on-going study to compare the cost-effectiveness of Plas vPET (virgin PET, a new resin) against that of rPET.
Consequently, the subcommittee suggested that the research team establish a testing center for contamination in rPET packaging so that private companies can use the service in submitting test reports to the FDA and testing institutes in order to apply for certification of rPET packaging process that is safe for food contact materials. In addition to generating income for the research center, it would also add value to rPET that can be safely used for food packaging.
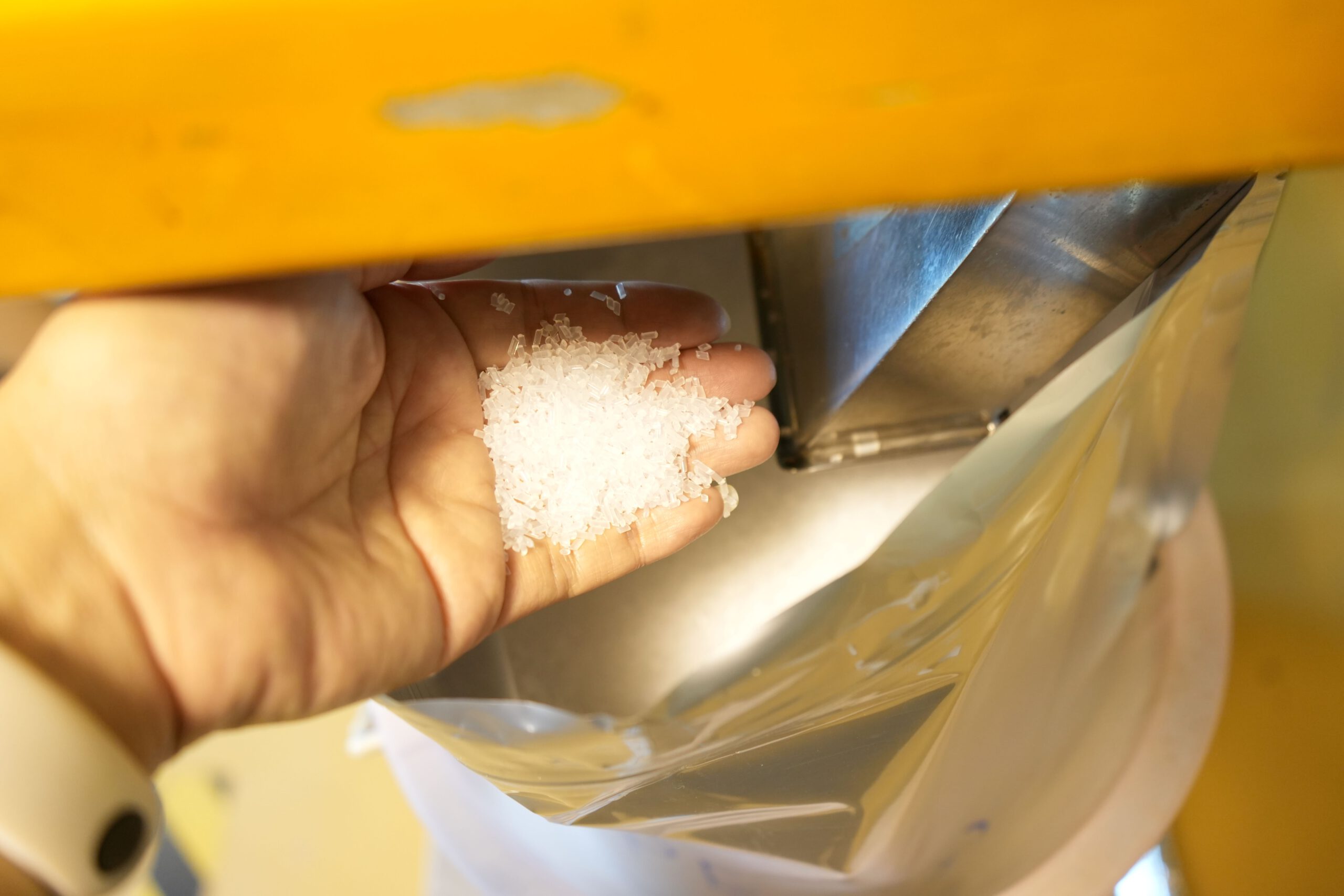
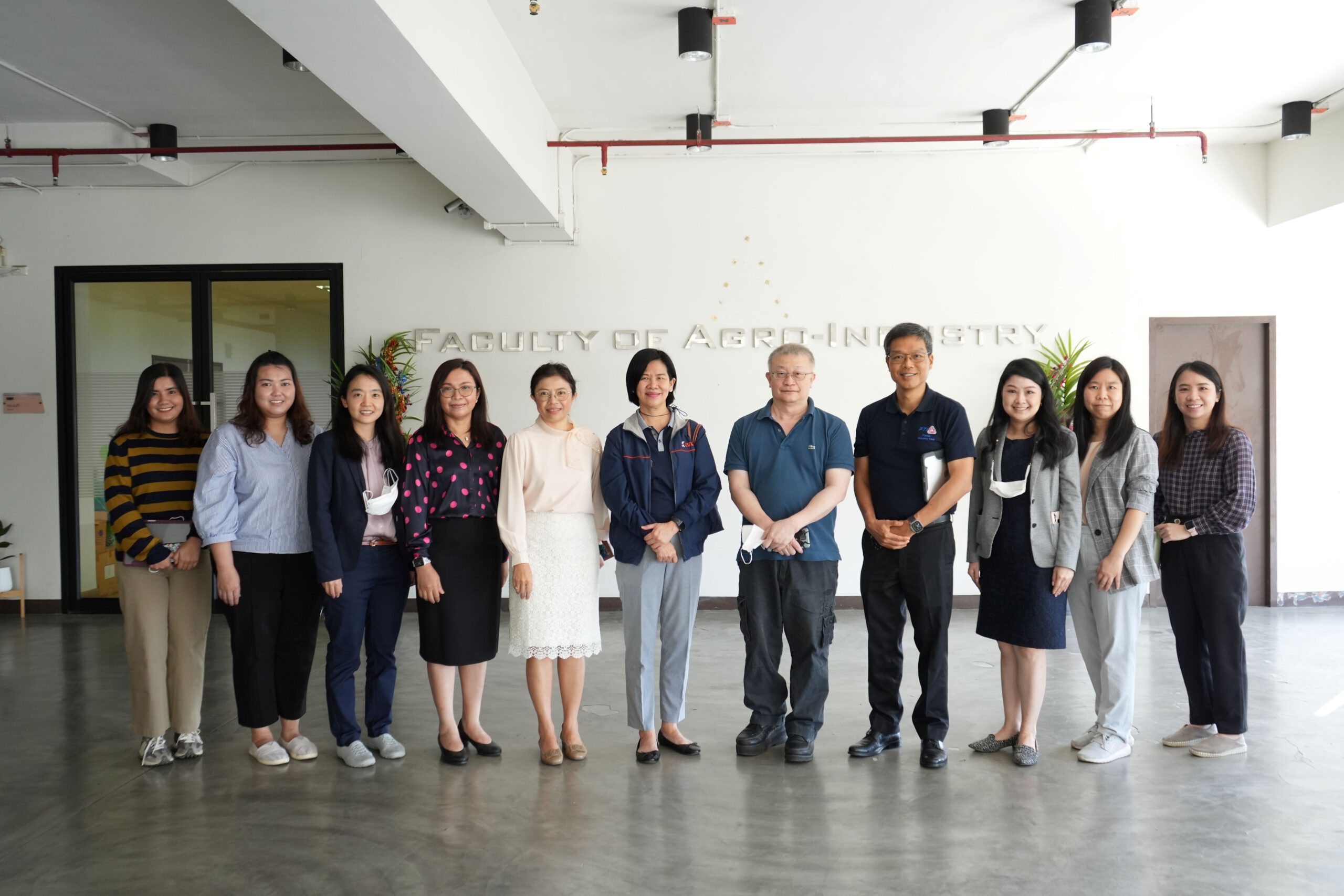
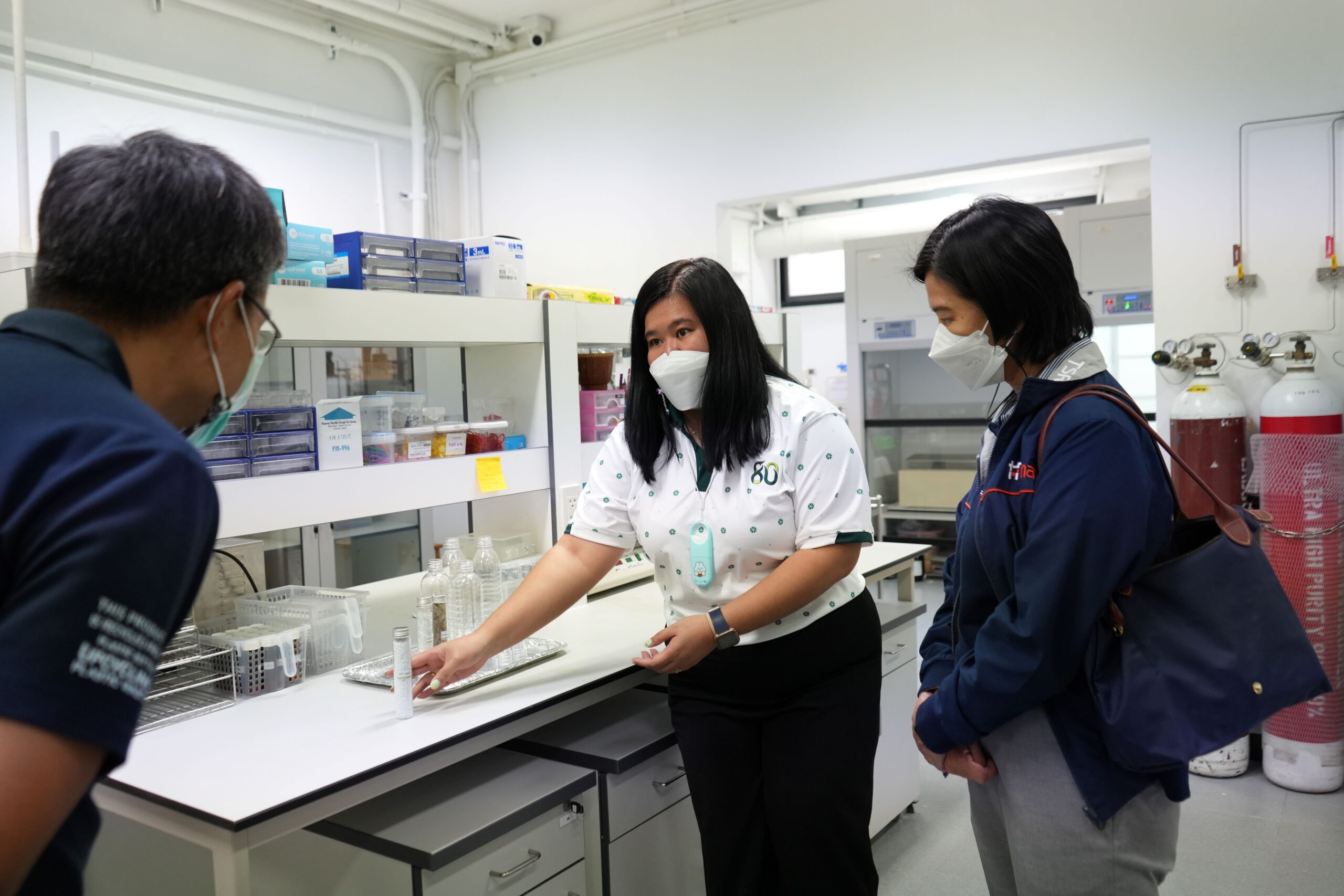
The project “Innovative prototype process for the production of artificial cellulose fiber (regenerated cellulose fiber) from high quality cellulose pulp (dissolving pulp) from waste materials in the pineapple industry”
Dr. Rangsima Chonlakup, project leader and the research team from Kasetsart University and Rajamangala University of Technology, Thanyaburi, are collaborating with Sang Charoen Grand Company, or SC GRAND, a co-investor, to study and develop a production process for high-quality cellulose pulp or soluble pulp from pineapple leaf fibers, which is the most abundant agricultural waste in Thailand available all year round. It can also provide pure cellulose fibers to add value by producing artificial cellulose fibers (regenerated cellulose), of which there are only two foreign companies in Thailand producing. The raw material used in the past has always been hardwood, and agricultural waste has not previously been experimented with.
This project has studied and developed the production process with properties suitable for forming lyocell and testing the physical properties, mechanical properties, and color absorption properties of moldable lyocell fibers. Additionally, research is being conducted on marketing information and production cost of lyocell fibers from soluble pulp produced from pineapple fibers. The research team received cooperation from farmers in Ban Kha district, Ratchaburi Province, in a joint venture to produce fibers from pineapple leaves with fiber scrapers. (decorticating matchine). Then the obtained fiber is boiled with alkaline pulping in a closed system and bleached at the Department of Textile Science, Kasetsart University. The soluble pulp is then used to form lyocell fibers by Dry-Jet-Wet Spinning method at the laboratory level at the Department of Textile Engineering, Rajamangala University of Technology, Thanyaburi.
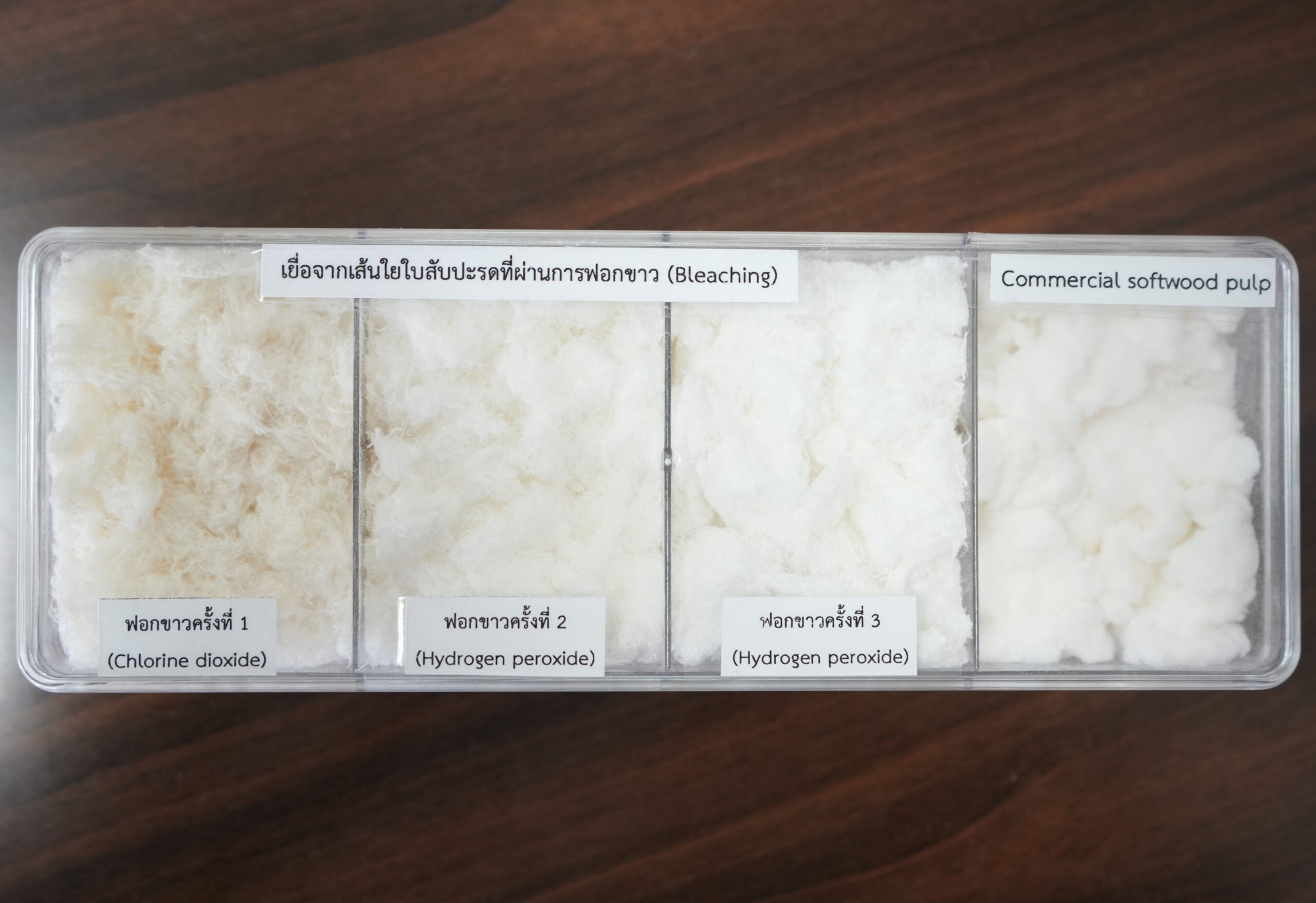
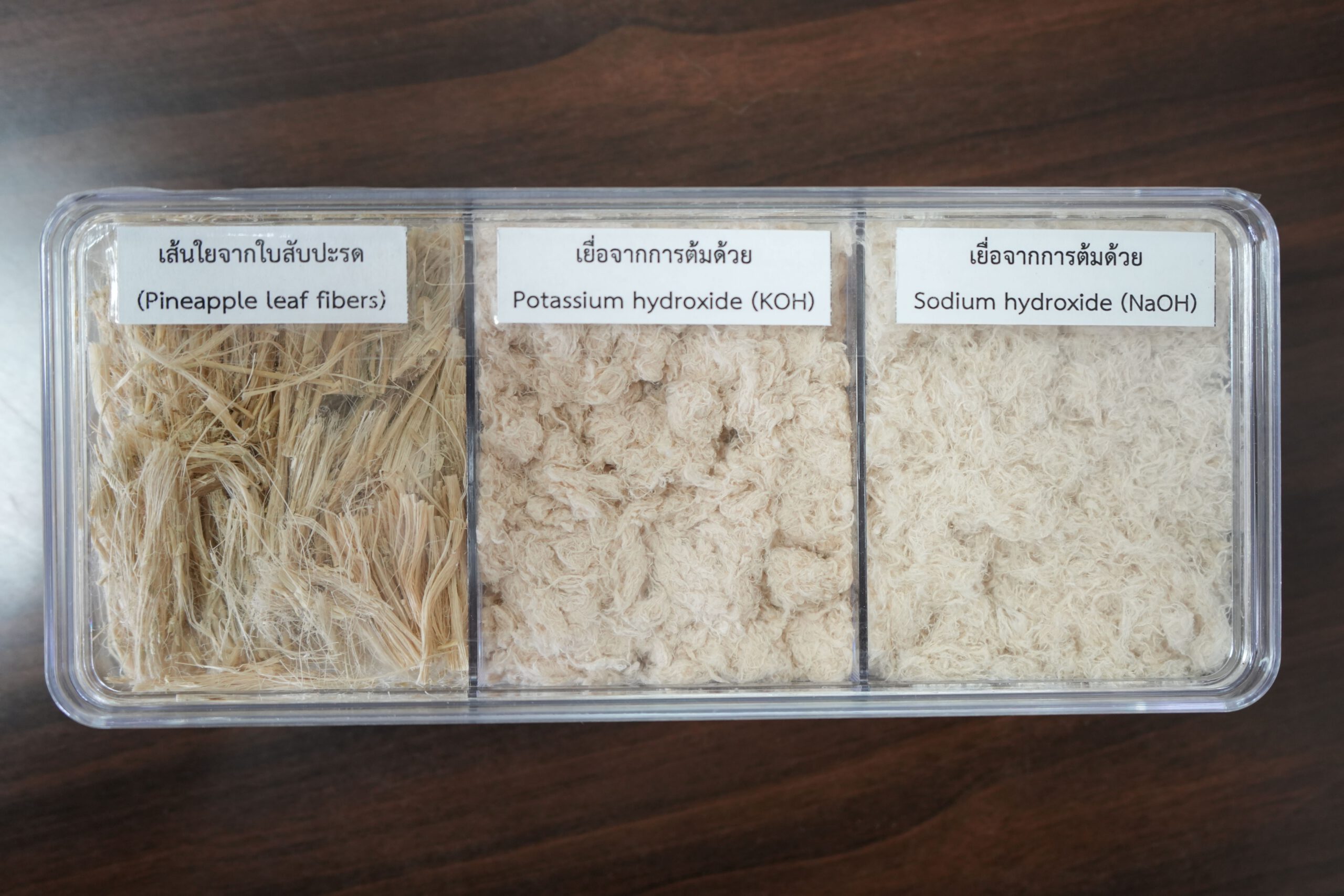
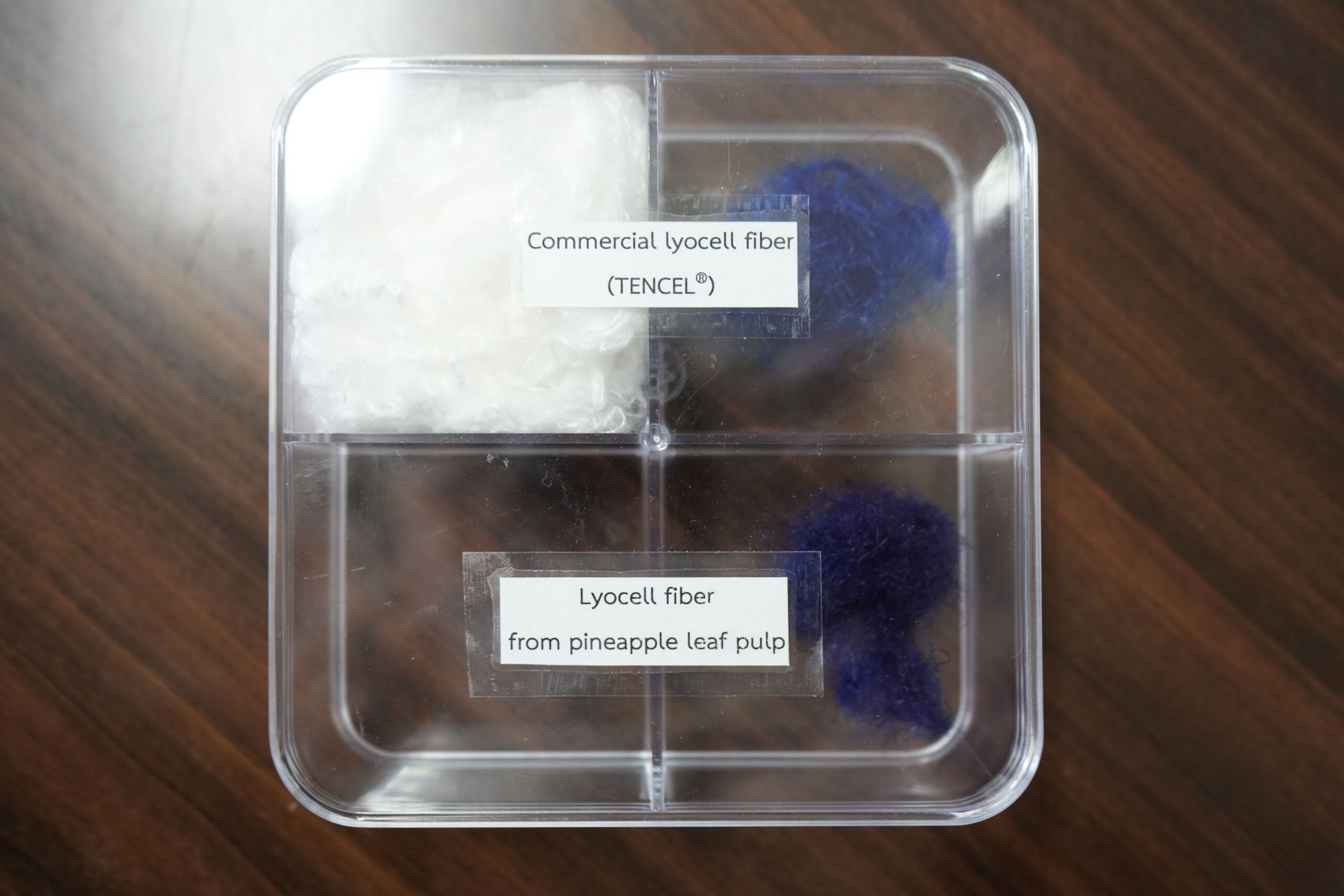
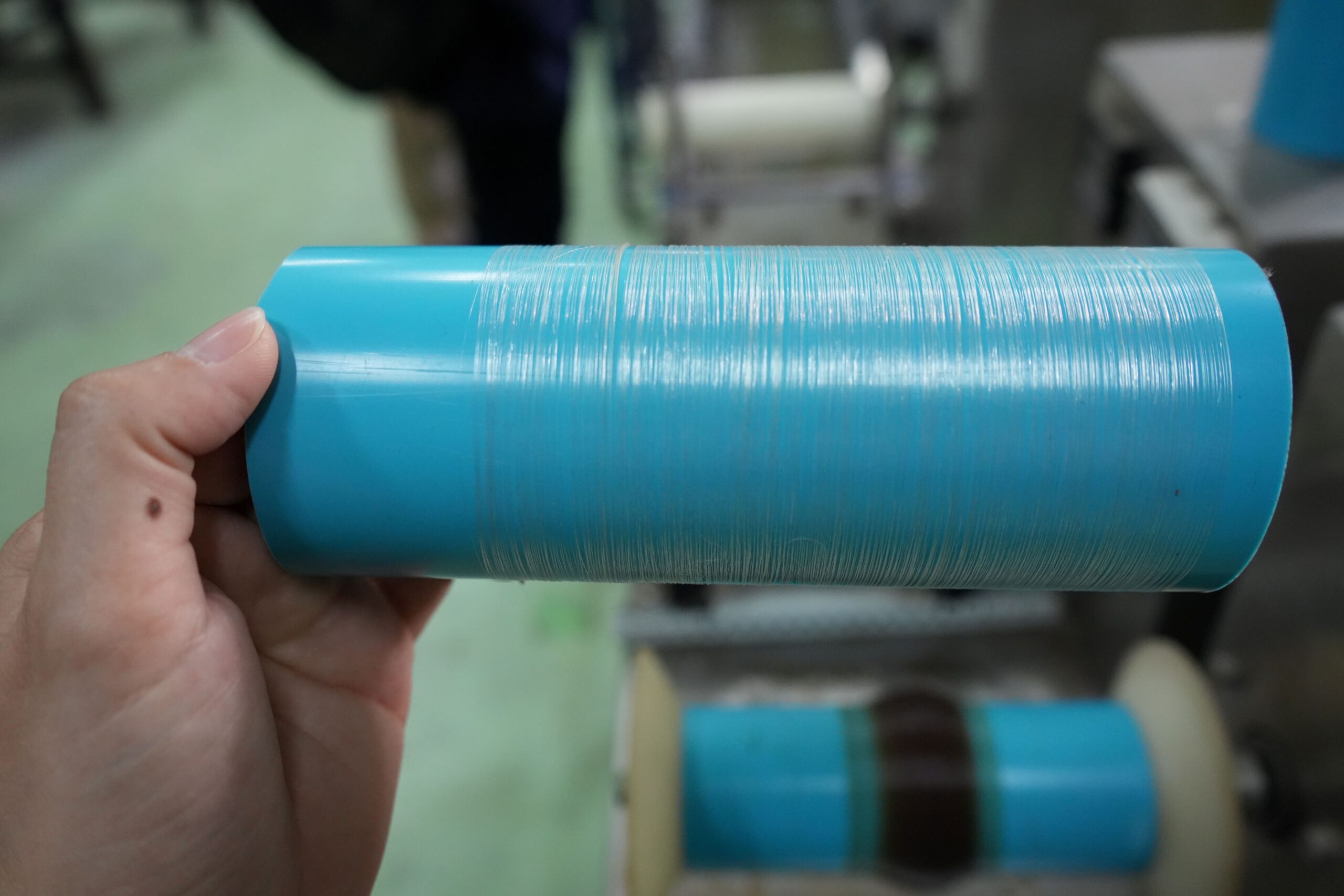
From the follow-up results, it was found that the research team was able to obtain the optimum conditions for pulping and forming laboratory-level lyocell fibers using the Dry-Jet-Wet Spinning method (in preparation for a utility patent application). When compared with samples of commercial softwood lyocell fibers and commercial lyocell fibers (TENCELL), the molded lyocell fibers were similar in density and color. It has a flat oval cross-section, and the diameter of the fibers becomes smaller with increasing rolling speed. But the diameter is still larger and has more shrinkage than commercial lyocell fibers and have chemical functional groups, as well as crystallinity property close to that of commercial lyocell fibers. Moreover, the heat stable tensile strength and the ability to absorb methylene blue was higher than that of lyocell fibers from commercial softwood pulps. However, a study of the production costs of dissoluble fibers from pineapple leaf fibers and the moldable lyocell fibers revealed productions cost of 719.25 baht/kg and 64,418.13 baht/kg respectively (when NMMO can be recycled up to 99.5%). During a market study of an eco-friendly T-shirt made from lyocell from pineapple leaf fibres, via online questionnaires, it was found that most of the respondents were interested in eco-friendly T-shirts that used fibers from pineapple leaves, which are agricultural wastes. But most respondents agree that the reasonable price is in the range of 601-800 baht. In addition, due to patent protection still in effect for lyocell fiber production, there are still very few manufacturers of lyocell fibers both domestically and internationally, which translates to higher cost to hire overseas companies to expand production capacity of lyocell fibers, far exceeding the researchers’ expectation. This is therefore considered a major obstacle that halted the implementation of the project.
However, the results of this study suggest the possibility of using pineapple leaves to make artificial cellulose fibers. We now have the knowledge for the production process, but it is still necessary to develop the technology to be ready for scaling up to commercialization, which, if successful, will help reduce waste in the agricultural sector, reduce the cost of handling very large volumes of pineapple leaves, due to Thailand being the world’s top exporter of processed pineapples. This also increases revenue from the sale of pineapple leaves, which are available throughout the season to supply the factory. This creates an alternative textile industry that is more environmentally friendly.

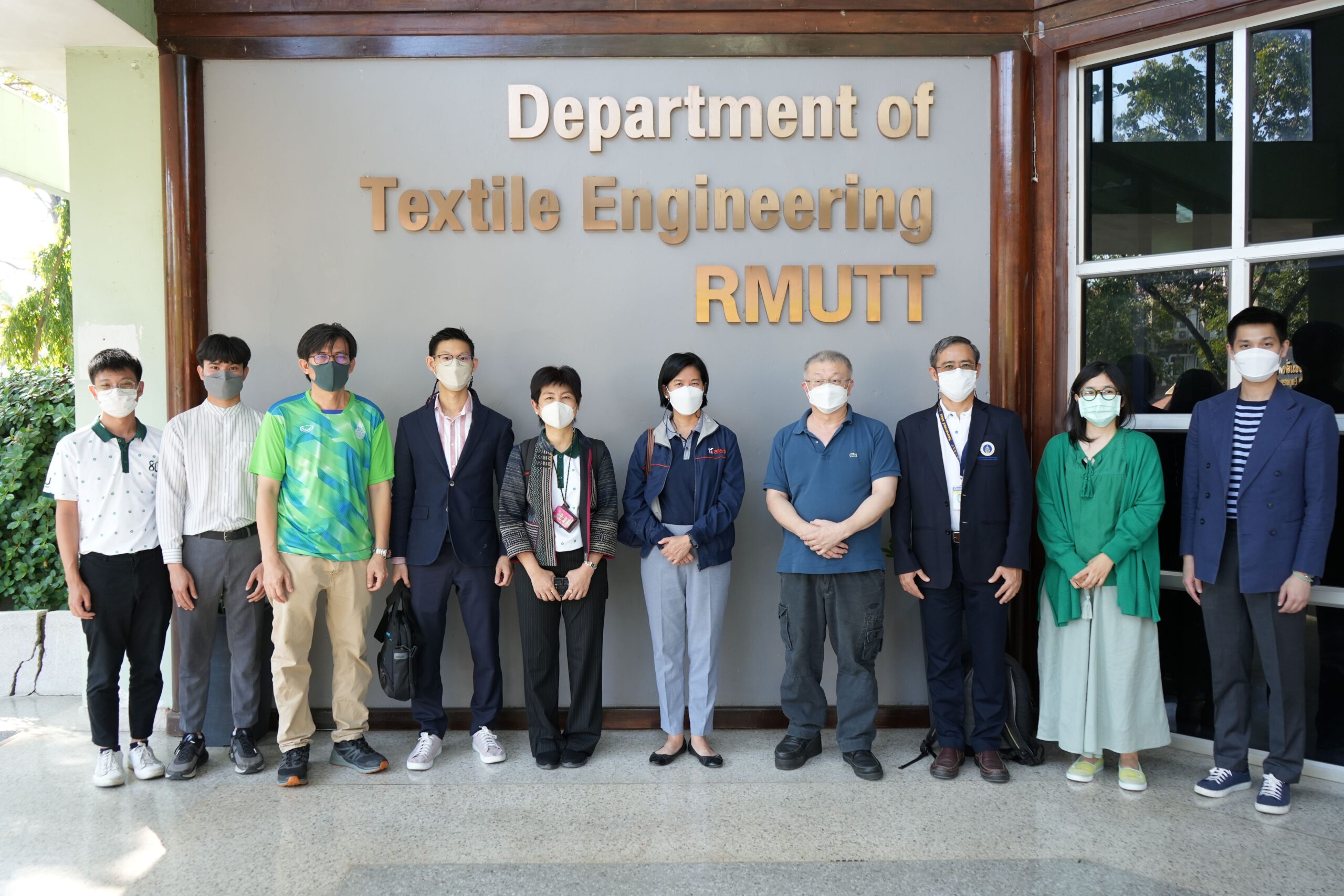
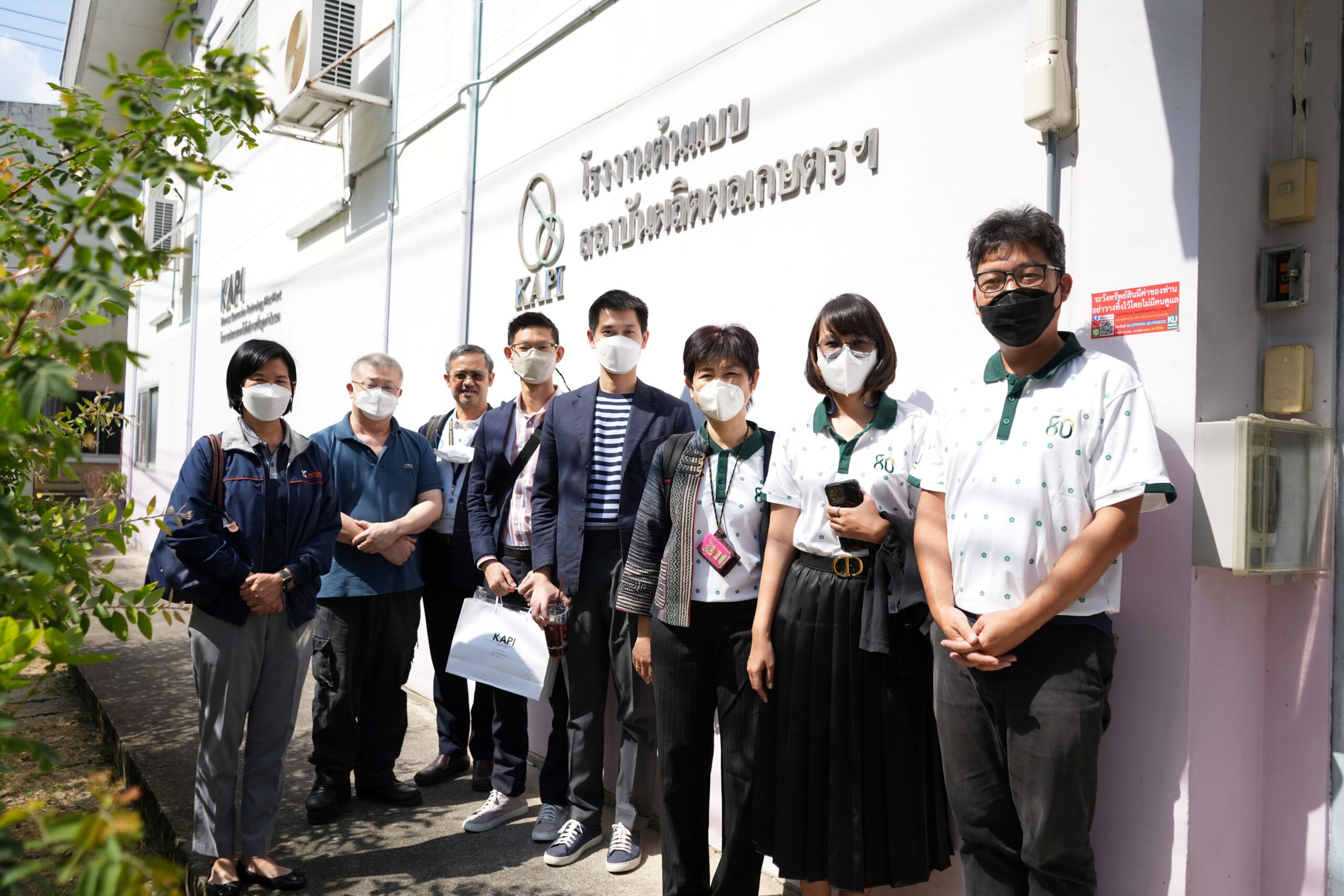
From discussions with Mr. Jiraroj Potchanawaraphan and Mr. Sanphat Pochanawaraphan, from Sangcharoen Grand Co., Ltd. (SC GRAND), which operates a spinning factory that specializes in recycling waste in the textile industry for 55 years, who are also co-investors in this project, it was found that although the project operation had to be discontinued due to the prohibitively high cost of expanding commercial capacity of lyocell fibers compared to what the research team had anticipated. However, the results of this project allow entrepreneurs see opportunities and development potential to expand on this knowledge and prepare for scaling up to enter the market in the future. That alone can be considered as a success, because it is proof that it is possible. We have seen a way to go further, though we still have to prepare many things. However, we see this as a good opportunity, thanks to the PMUC for granting us the funding with which conduct the research, benefiting from trial and errors. This can help many entrepreneurs, especially smaller entrepreneurs, who want to research and develop products to expand the scale to larger markets. So even if the project had to be terminated, for us it was all worth it,” said Mr. Jiraroj.
Visiting the site to followup on this project allowed the subcommittee to see the problems faced by the research team. And consuquently the subcommittee provided suggestions and guidelines for submitting proposals to request research funding to further build on knowledge gathered during the project.
The Project “Innovative hemp-crete wall building material with decorative surface using hemp cores from Thailand for commercial use.”
Dr. Rangsima Chonlakup, project leader and the research team from Kasetsart University, Rajamangala University of Technology, Thanyaburi, Rajamangala University of Technology, Lanna, Tak, and Rajamangala University of Technology, Isan, all entered into a partnership with DD Nature Craft Co., Ltd. (joint investor) to develop innovative building materials for commercial pre-cast hemp-based concrete walls using hemp fibers in Thailand. The hemp core is a by-product from the hemp plantation process from peeling the bark to produce fibers for use in the textile industry. In foreign countries, it is used to produce lightweight bricks called “Hempcrete” by mixing crushed hemp core and using hydrated lime as a binding agent. The strains of hemp cores in foreign countries are different from those in Thailand. A new formulation must be studied and researched using domestically grown hemp cores and cement binders mixed with gypsum plaster in order to produce formulas for lightweight concrete blocks with working strength which passes the TIS quality standard.
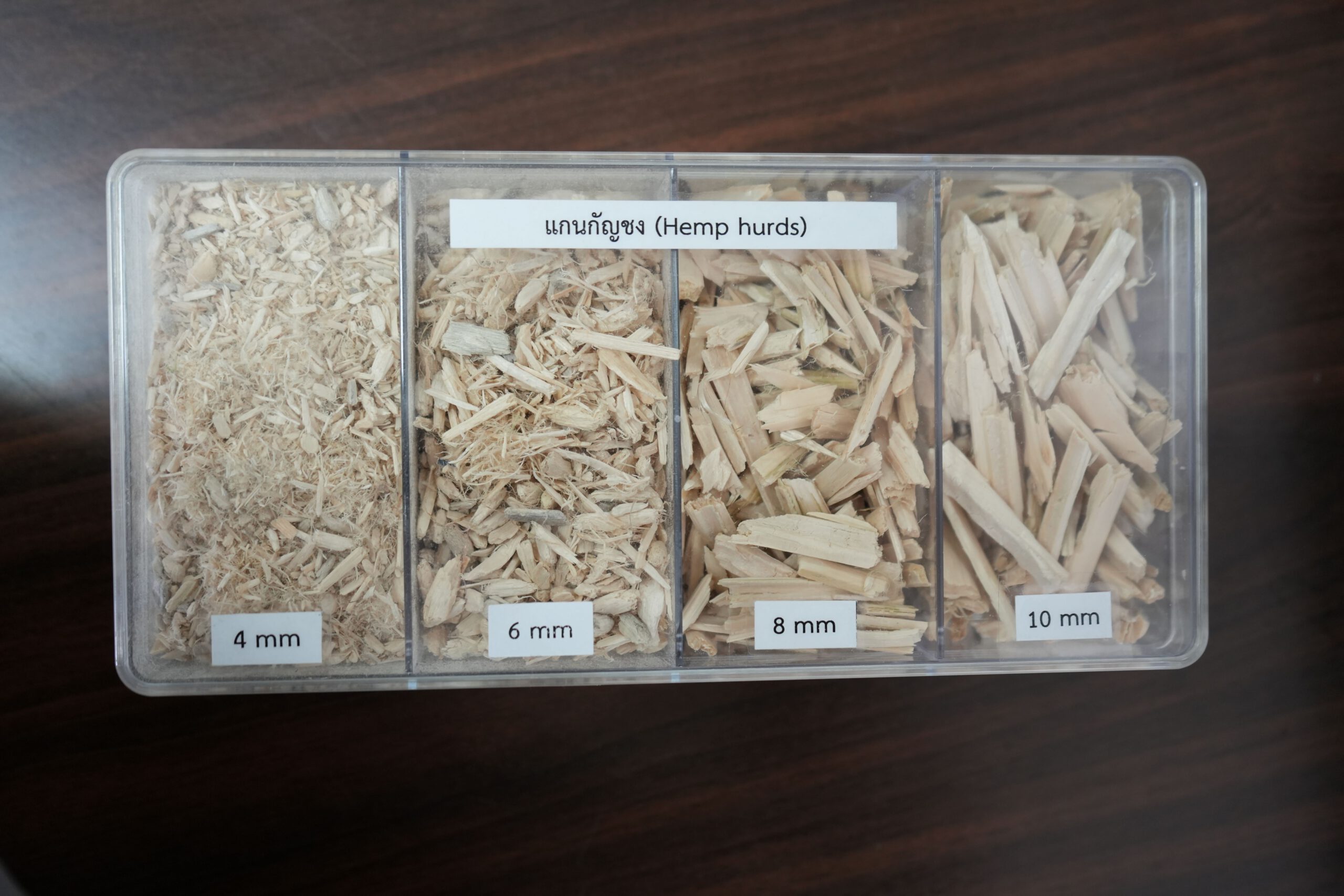
This project is aimed at developing the production process for hempcrete products (Aerated concrete blocks mixed with crushed hemp core) used in wall building materials to be stronger and lighter in weight, meet TIS 2601 standard. The ultimate goal is to eliminate the disadvantages of hemp concrete products developed by the research team, which were strong but not light weight because they use cement as a binder. In addition, the disadvantages of traditional hemp concrete products that the joint venture company can currently produce, include being light in weight but not very strong due to using gypsum as a binder. Then there are the disadvantages of hemp concrete products from abroad, which are lightweight, strong, but take a very long time to cure (about 1 month), because hydrated lime is used as a binder. In this research, a new binder formulation was developed for the first time, using cement together with gypsum plaster, which has passed preliminary testing in the laboratory.
In this study, the research team used Portland cement type 1 and gypsum plaster, at one-to-one ratio, and using finely crushed sand as an added ingredient to boost strength. (The cement helps add strength, while the gypsum plaster helps to speed up the curing process.). This makes for a much less complicated process, faster hardening, lighter weight, higher strength and durability as well as good thermal insulation. In addition the development of hemp-based wall building materials that are unique by mixing hemp core of various sizes into ready-made plaster for plastering aerated concrete walls to make decorative patterns.
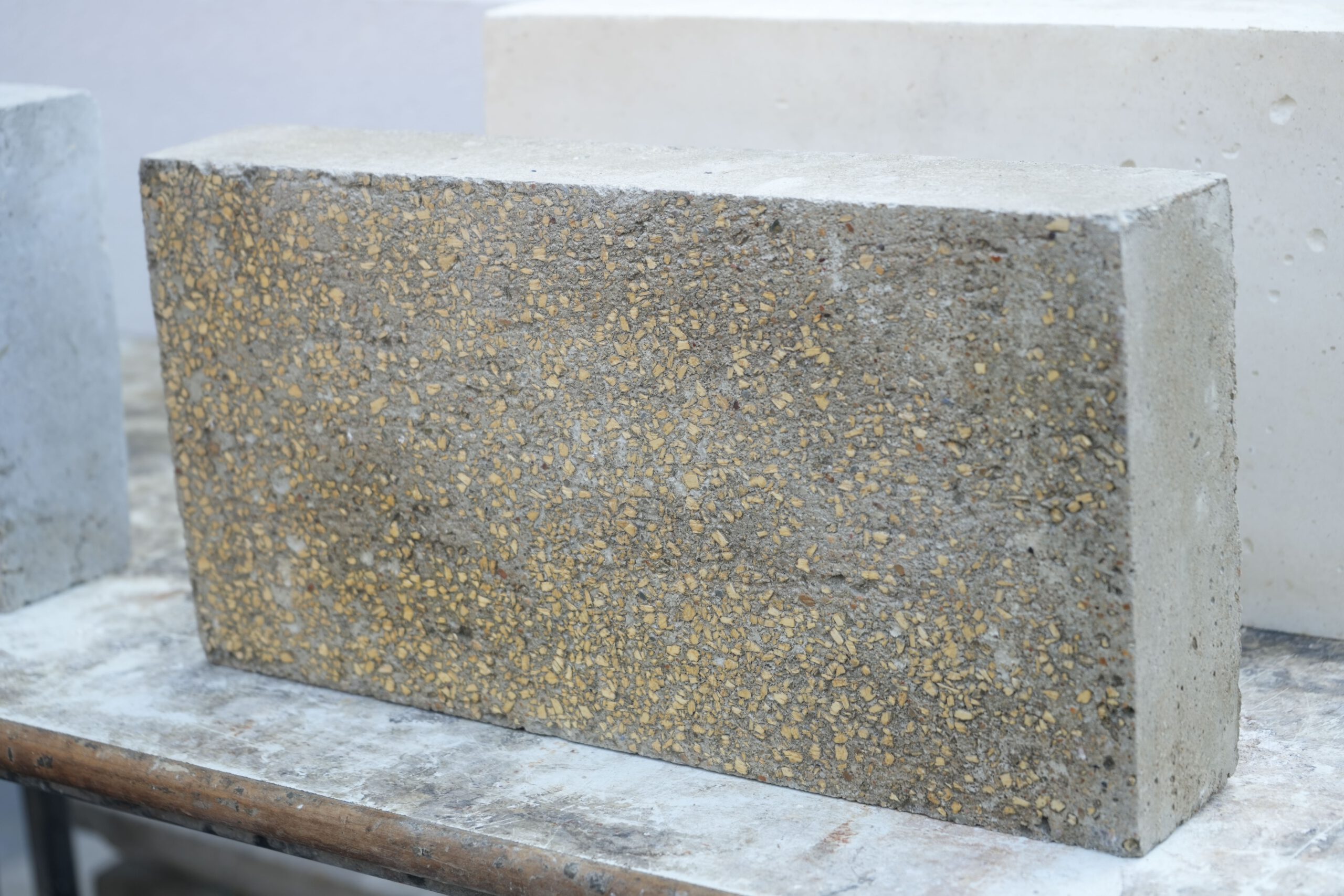
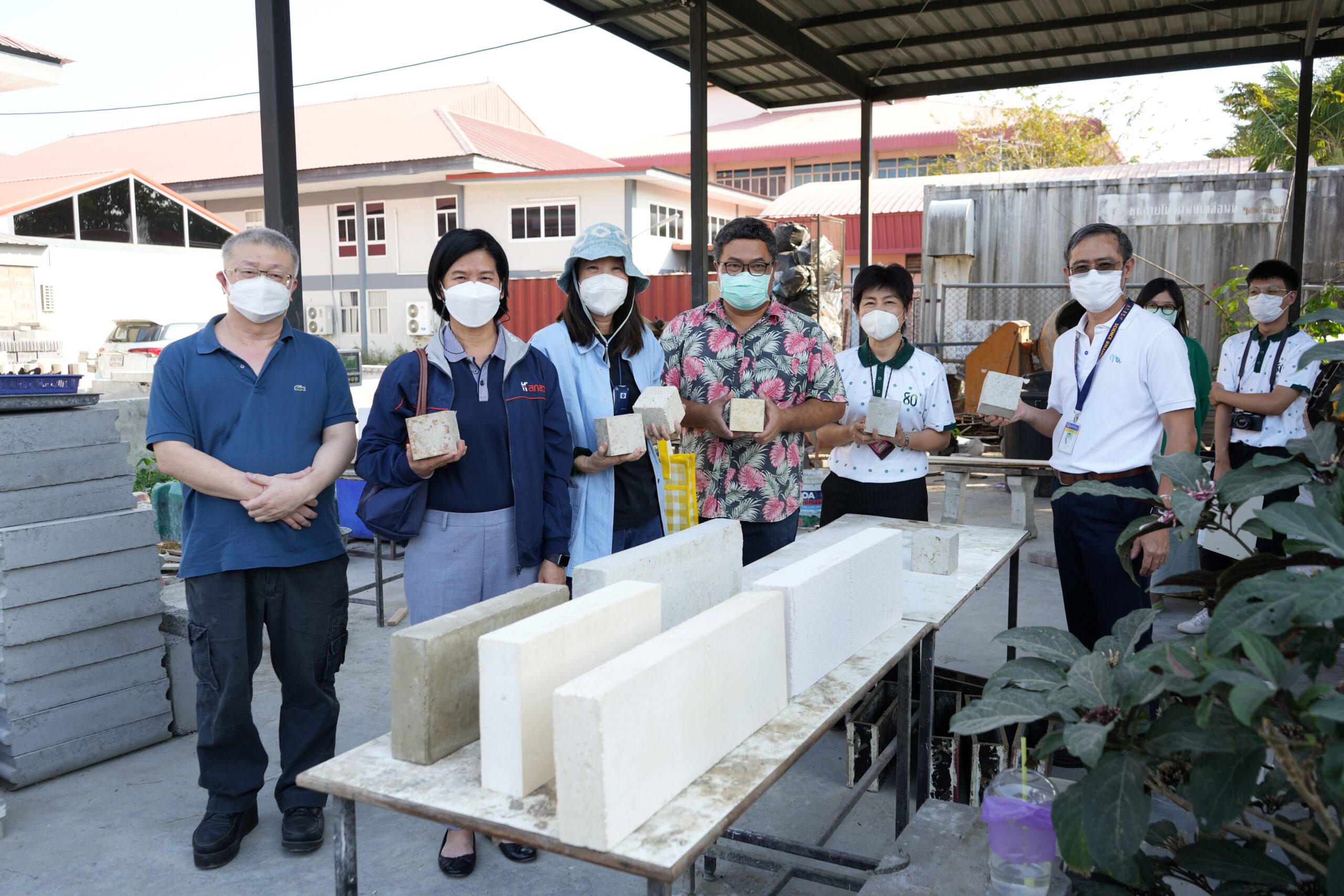
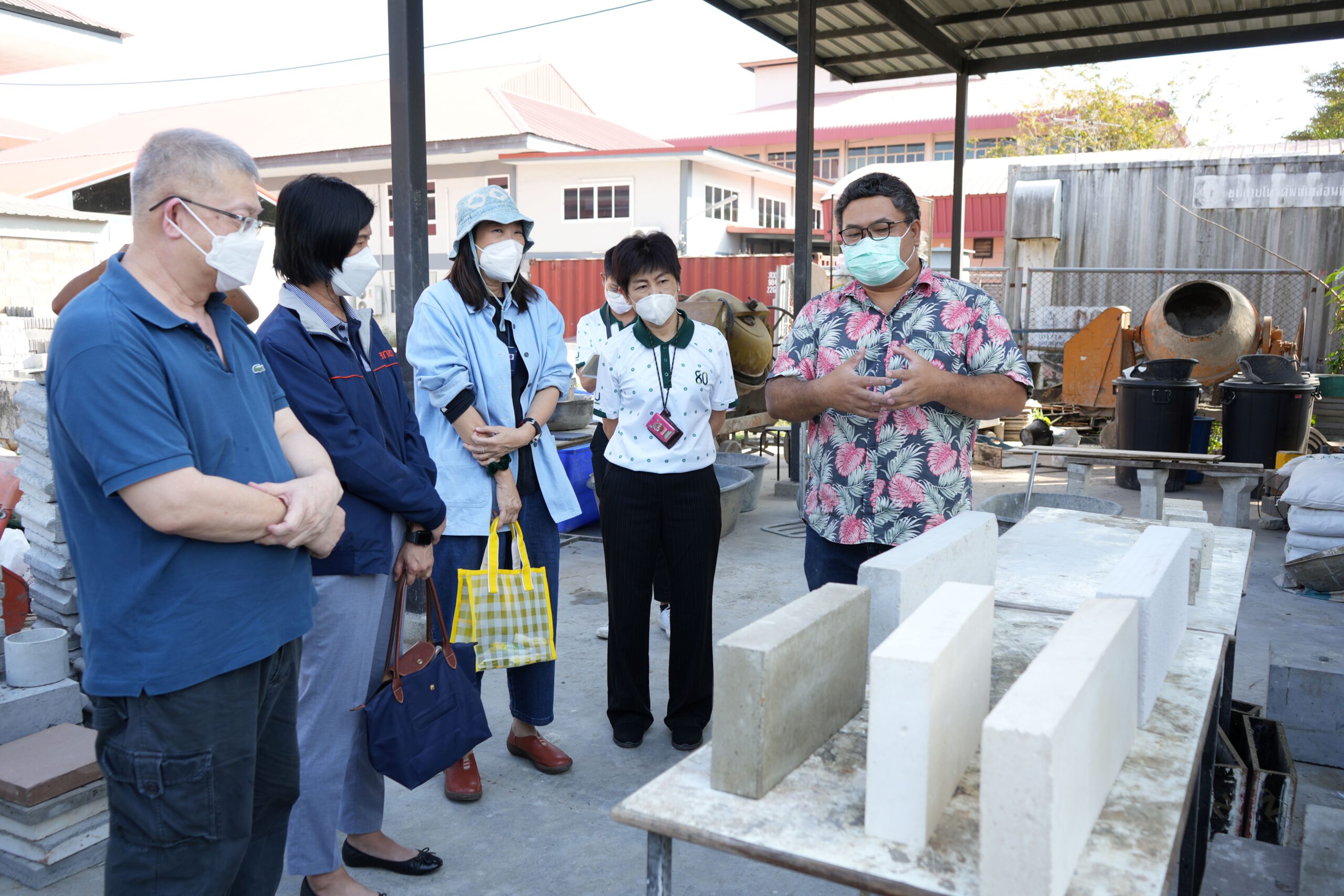
The technology developed from this project is a combination of advantages of each technology into a new technology that can improve hempcrete’s properties in terms of weight and strength, which led to passing the TIS standard, something never before accomplished in Thailand. Additionally, the production process became easier and the production cost is also lower, making very much suitable for the companies co-sponsoring the project and can be extended to SMEs and the greater community.